PERSPECTIVE
Creating wearable art : Challenges in Ecoprinting
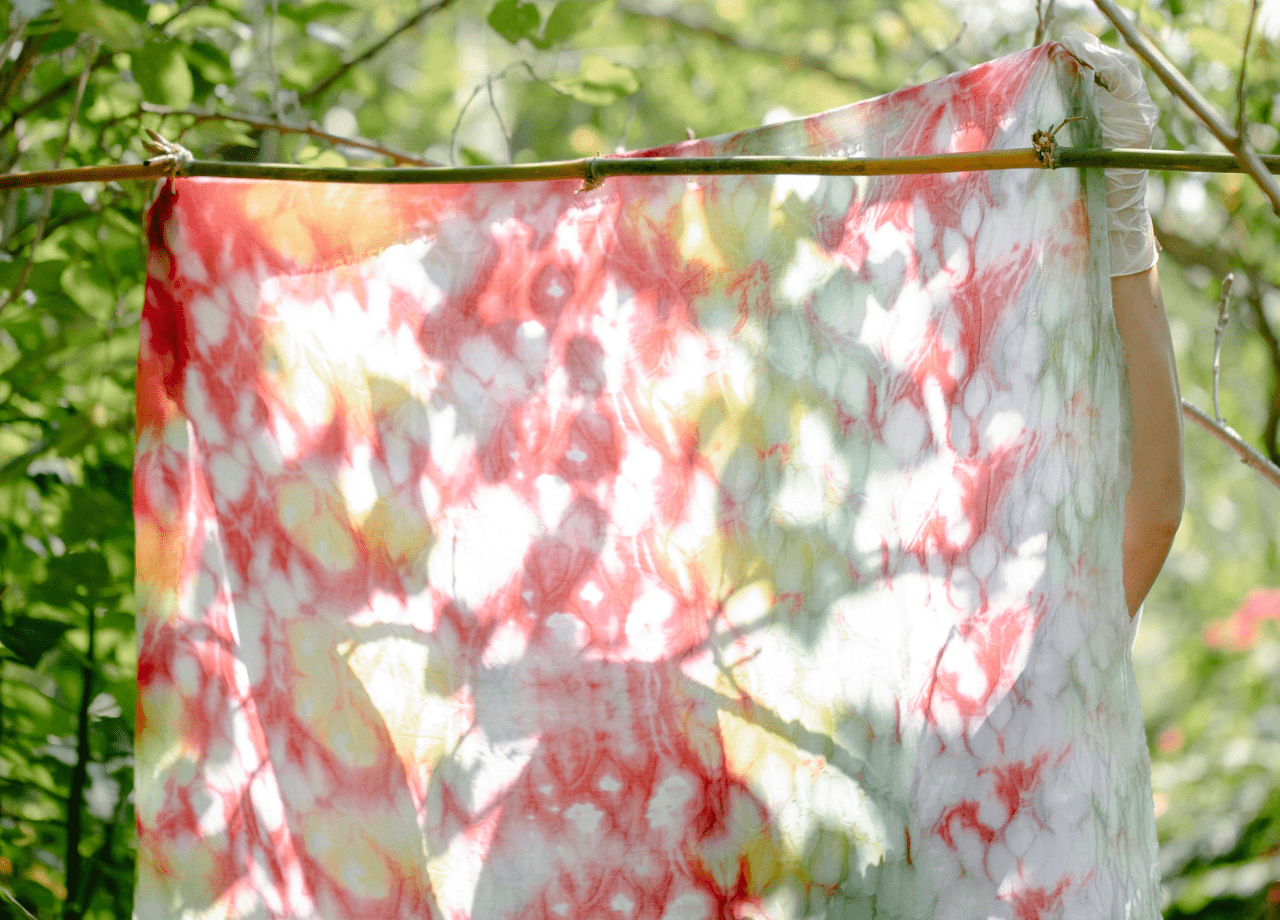
How do artists balance their creative process while managing customer expectations?
Cirana Earth focuses on brands that are working solely with natural colours and natural materials. The cornerstone of many of these brands are entrepreneurs, passionate about working with natural colours, usually adept at the practice or just starting out. It’s the entrepreneur’s passion that results in the start of brand that embodies their creative expression.
Artists and experimentation:
While creating art is an intellectual pursuit informed by an individual’s experiences, working with natural colours is complex. Experimenting is a way of learning and building deeper knowledge and skill in this space. Creating art with natural colours is a confluence of two streams that requires experimentation as well as imagination.
We all know that experimenting can be tedious and time consuming as it is satisfying. While creating art is unique to every artist, the commonality in every artist’s pursuit is that their output is subject to managing a few intangibles like creative expression and customer expectation with finite elements such as time and resources. So, if that's the case can the end results be artistic? or are they mundane? The end results are beautiful to behold, unique and enter the realm of wearable art but it’s the journey that is often laborious and sometimes overlooked. What does it take for the artist to achieve these stunning results? How do they manage the complexity? Are the results always worth the effort? Let’s explore this aspect through the work of a creator/entrepreneur whose label works with natural materials and natural colours, with a focus on sustainability.
Context:
Eco printing is a contact printing method where flowers leaves are treated with a mordant and their colour fast images are printed onto fabric creating unique patterns and colour schemes. “Plant material bundled inside of cloth is steamed or boiled to release the dye found naturally inside the plant, creating a contact print in the shape of the leaf or flower used” Heat releases the dye out of the plant, colouring the fabric next to the leaf. The colours are revealed as the plant material is lifted off the unwrapped fabric- Sharlene Bohr Eco print artist USA.
Experimenting with dyestuff:
Eco printing creates unique results every time and so it lends itself to customisation. In order to create the colour palette desired by the client, Kalpana, the artist featured in this article, chose to work with a flower that is not usually used for eco printing. First trials on swatches yielded a beautiful result and the client was thrilled.
Process
Step 1: Experimenting with dyestuffs: Creating Swatches
Kalpana created a few swatches based on the clients brief and shared images of the swatches she had created. The first couple of swatches were created using Marigolds and dried Indian rose petals on mulberry silk and last one using with red and pink Gerberas. The lustre and colour given off by the Gerberas seemed to produce the most desired effect and the commission was confirmed with Pink Gerberas as the main eco printing ingredient for her creation. Kalpana knew that despite the excitement there were bound to be challenges while producing a 5 metre garment and also knew to expect difficulties while extending the scale of working with a lesser known flower.
|
![]() |
Step 2: Process: Experimentation continues :Pattern Creation
Handloomed Mulberry silk was chosen for creating an eco-printed saree. The fabric was chosen because of its light weight, durability and innate lustre. Full-scale trials had to be carried out on handloomed mulberry silk and if the outcome was not as desired then all the steps would have to be repeated using/reusing virgin cloth which is quite an expensive proposition for the artist.
Initially the fabric was soaked in warm water for half a day. Then, the fabric was scoured with a Ph neutral soap of the artists choice. Scouring removes starch and any other impurities from the fabric that may have set in during the weaving and yarn production stages that could cause the natural dye present in the plant material to not fix or not adhere uniformly or cause undesired colorations in the fabric. Then alum, a naturally occurring mineral salt with medicinal properties known as or fitkari in Hindi (Potash Alum) was used to mordant the flowers and the fabric. The fabric was soaked in 10% alum solution for a day. The flowers were mordanted just a few hours before eco printing.
Time taken:
Preparation:
Pre treatment half a day
Socuring half a day
Mordanting 1 day
Step 3: Process : Eco printing:
The customer had requested for a saree this time and that usually means being able to distinguish between the body (part of garment that wraps around the body of the wearer) and the pallu ( the remnant fabric that hangs of the shoulder of the wearer making for a beautiful display) .
Creating this particular distinction between the two regions of the garment was the most challenging task for the artist. The task was to create not one but two unique patterns, for the two separate regions of the garment using Gerbera flowers. The suitably prepared flowers were arranged artistically along the body and Pallu area of the experimental fabric and plastic film was used to roll the garment tightly and the garment was secured. Next it was set in a large steamer and allowed to steam until the desired effect was obtained. The eco print pattern would emerge only when the fabric was cooled and the plastic film removed. The artist usually has little or no control of the vibrance and intensity of the eco print in this final stage.
Time taken:
Flower mordanting – few hours
Eco printing – Few hours
Post process final rinse (Including the time taken for Shade drying)– Few hours, an hour or two
Total time taken - Roughly half a day.
Step 4: Process: Experimenting with the outcome
The entire process from pre-treatment of the fabric to unwrapping the plastic film after eco printing takes anywhere from 3-4 days. The quality of the outcome is very subjective in this process. It is subject to several immeasurable factors such as the artist’s experience of working with the dye material and the artists unique impression of beauty and finality. In this specific case the outcome was also dependent on the commissioner or the customers idea of beauty and perfection. The artist created nothing less than 4 versions of the saree, causing the time and costs to be increased by a factor of four. To arrive at the outcome, the artist had to finely balance all their efforts with frequent communication to the customer.
Managing process complexity through communication and inclusion:
While the freedom to create and experiment draws artists and entrepreneurs to natural colours, working in real time presents certain challenges that can many times be overcome with clear communication and customer inclusion.
In this case the artist kept in touch with the customer and educated them throughout the process. Right from preparing swatches with different subject flowers, to sharing information every time an experiment failed, the artist kept the customer informed. Fortunately for the artist, the customer was supportive of the time taken and the experimentation required to create a floral pattern on the fabric of their choice. An indication of the cost was provided to the customer at the start of the process and the effort for subsequent iterations was also added to the final cost. There were no surprises for the customer and they felt included into the artists creative journey. This step was key to the success of this experimental creative endeavour.
Appreciating naturally coloured products:
Hopefully this article gives the reader a glimpse into the artists exacting creative journey while creating a customised naturally coloured, eco printed garment. The work takes several hours of intense labour. Experimenting with natural materials is a creative, lonely and time intensive process that is at the core of natural dyeing and working with natural colours. Experimentation is integral to the artists understanding of working with materials and dyestuffs of their choice.
For all our readers out there, developing an understanding for this process is imperative to nurturing an appreciation for naturally coloured objects. Additionally, keeping a customer in the know also brings in transparency and leaves no room for miscommunication. This time the outcome was definitely worth the effort.
Kalpana was drawn to organic textiles and working with natural materials. Her research made it clear to her that working with natural materials and fabrics would suit her creative expression the best. She chose natural colours as her medium, her contribution towards trying to produce consciously crafted clothing.
Entrepreneurs such as Kalpana have taken a leap of faith to tread the path traversed by few. They have invested their time and efforts towards nudging customers and consumers to make balanced consumption choices by using their personal, creative energies and experimentation as the tool. The customer was delighted with the 4th eco-printing outcome while the passionate artist was not yet satisfied! I think it’s safe to say that the pictures speak for themselves.
(The extra fabric dyed during her experiments have been responsibly used to create other smaller garments in Kalpana’s portfolio keeping in line with the brands approach to creating little or no waste)
Please write to info@ciranaearth.org for further information about eco printing or to connect with Kalpana.
"Each trial of eco-printing would be different from the other. Slight changes in the process can alter the final product "- Kalpana, Gaia Fashion House
Similiar Stories
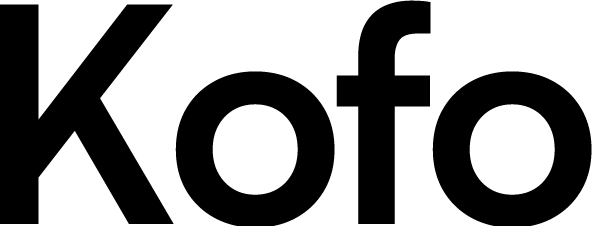
Kofo is an award UI/UX designs and branding
agency based in New York, USA.